Robust Sensor Design and Optimization
Focus Design
- Simulation of variable geometries using Computer Aided Engineering (Finite Element Simulations)
- Modelling of Systems considering uncertainties
- Uncertainty-, Sensitivity- and Feasibility – Studies
- Design and application of Designs of Experiments (DoEs)
- Response-Surface-Methoden to determine sources of variation
- Explorative designs to completely cover the design-parameterspace
Focus Optimization
- Minimization of unwanted variation due to
- Geometry properties
- Materialparameters
- Environmental influence (e.g. temperature, moist …) etc.
- Maximization of variation due to the quantity of interest (measurand)
- Linear dependence on the measurand
Distribution of designpoints using explorative (space-filling) Latin-Hypercube design.
Simulation-setup for evaluation of a capactive position measurement of micromechanical mirror. Due to symmetry, simulating a quarter of the geometry is sufficient.
Simulation-setup to evaluate a 3D- and inkjet-printed capacitive sensor.
Motivation und Aims
The robustness and quality of products in general, und sensors specifically, may suffer significantly from variation of the following quantities:
- Materialproperties,
- Fabricationprocess (e.g. 3D-printing and inkjet-printing),
- Variations in geometry,
- Environmental influences (temperature, moist, etc.)
To analyse consquences of such variations, and to be capable of predicting them through appropriate models, allows to optimally adjust controllable parameters, as well as to minimize unwanted influences such as environmental conditions or uncertainties originating from the production process. Computer-aided robust design, employing Finite Element Method (FEM) simulations, based on specifically developed DoEs, and model-building, targeted at an optimal analysis and description of design-parameterspaces and simulation results, are thus main focus areas for research and development with, at the same time, high relevance for the industry.
Publications
Diagnostic Coverage Estimation Method for Optimization of Redundant Sensor Systems
Wolfgang Granig, Dirk Hammerschmidt, and Hubert Zangl. Diagnostic Coverage Estimation Method for Optimization of Redundant Sensor Systems, IEEE Sensors, Glasgow, Schottland, 29. Oktober-1 November 2017
Feasibility Considerations on an Inkjet-Printed Capacitive Position Sensor for Electrostatically Actuated Resonant MEMS-Mirror Systems
Design of a Fast, High-Resolution Sensor Evaluation Platform applied to a Capacitive Position Sensor for a Micromirror
Design of a Fast, High-Resolution Sensor Evaluation Platform applied to a Capacitive Position Sensor for a Micromirror
Current Projects
Posititionsbestimmung von mikromechanischen Spiegelsystemen mittels Ink-Jet Technologie gedruckter Sensoren.
Projektleitung
Hubert Zangl
Projektmitarbeiter:innen
Lisa-Marie Faller
Laufzeit
01.12.2014 - 09.02.2018
Förderung
Österreichische Forschungsförderungsgesellschaft mbH (FFG)
Posititionsbestimmung von mikromechanischen Spiegelsystemen mit mittels Ink-Jet Technologie gedruckter Sensoren.
Kooperationspartner:innen
You can find a complete list of all Research Projects of the Institute of Smart System Technologies in the Forschungsdokumentation (FoDok).
Quicklinks
Portals
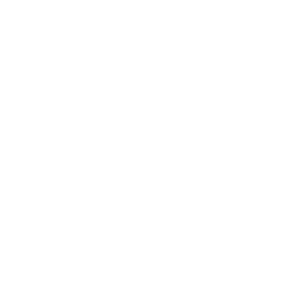
Information for
Address
Universitätsstraße 65-67
9020 Klagenfurt am Wörthersee
Austria
+43 463 2700
uni [at] aau [dot] at
www.aau.at
Campus Plan